INVENTORY CONTROL: The Standard Cost Inventory Valuation System Series
In Certain Standard Cost Systems, Variances May be Summarized by Work Order
A work order is a document that provides specific instructions to produce a product or complete a specific task, usually for a specified quantity.
Work orders are commonly used in so-called “job shops” – manufacturing plants that produce specific products for specific customers in accordance with custom specifications, based on purchase order quantity. The purchase order (or other criteria) may specify the standard work order quantity. The work order would have an associated standard quantity of raw material, labor and overhead necessary to produce the standard work order quantity. The work order would also specify the corresponding costs. Differences between the standard quantities and costs associated with the work order and the actual quantities and costs associated with the work order are reflected as work order variances.
What Variances Should You Expect to See in a Work Order Standard Cost Environment?
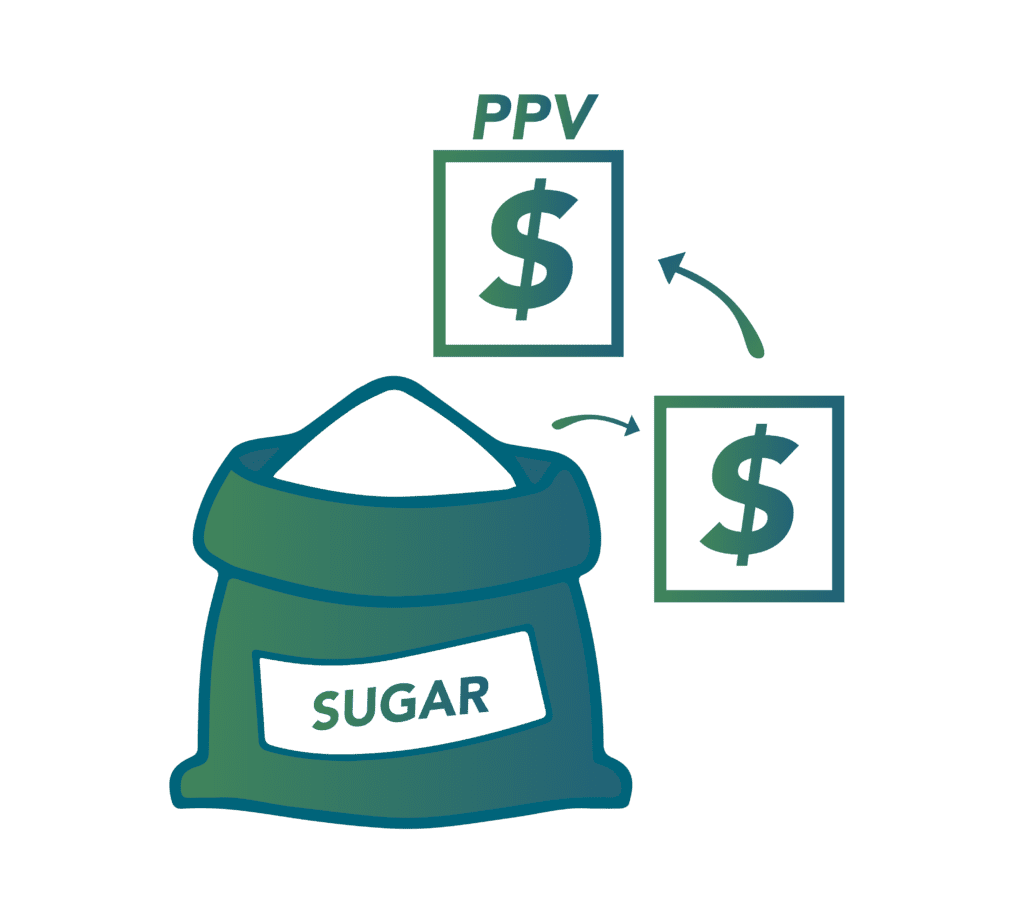
Purchase Price Variance
For purchased items (raw material or purchased goods), if the standard cost differs from the actual purchase price, you will have a purchase price variance (PPV). When you receive a purchased good/raw material, your accounting system will update the accounts payable account using the price on the invoice. However, the inventory account will be updated with the standard item cost. The difference between the two costs is a PPV.
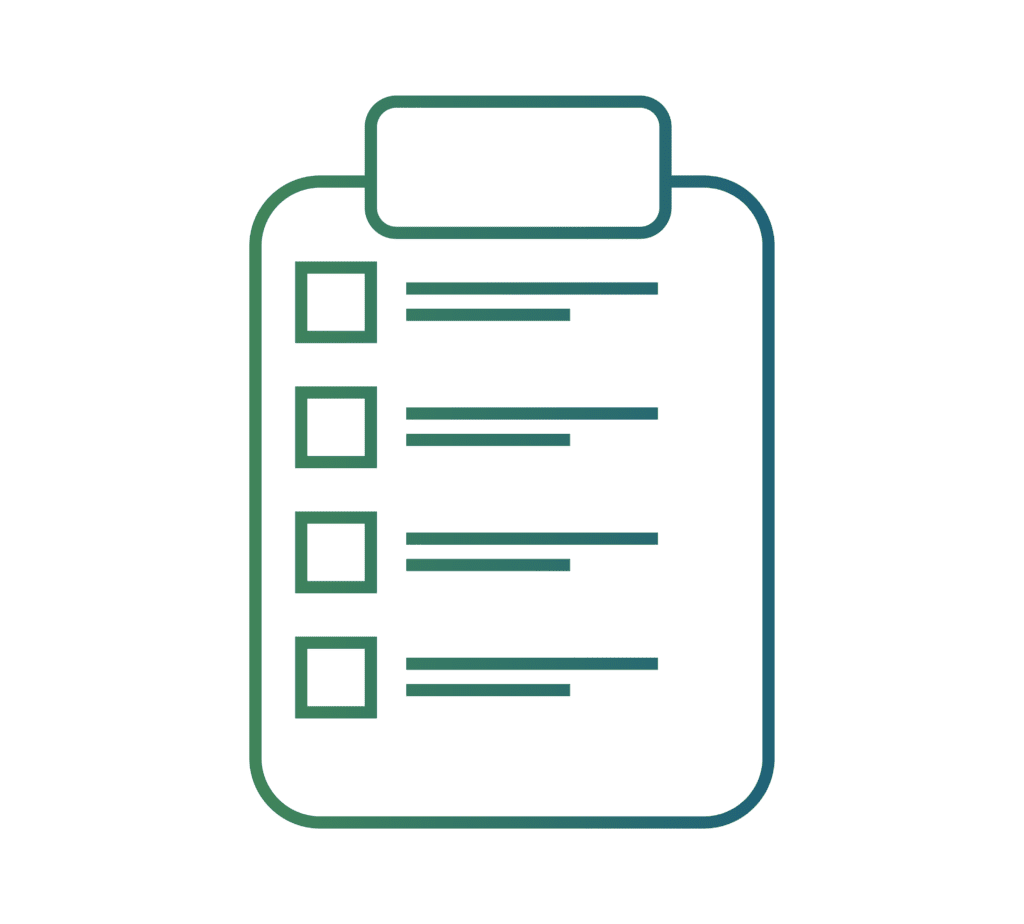
Work Order Variances
The variance on a Work Order (WO) in a standard cost division will be the difference between the value of the Labor, Material and Overheads charged to the Work Order compared to the standard cost of the item being produced on the Work Order.

WO Material Variance (Usage)
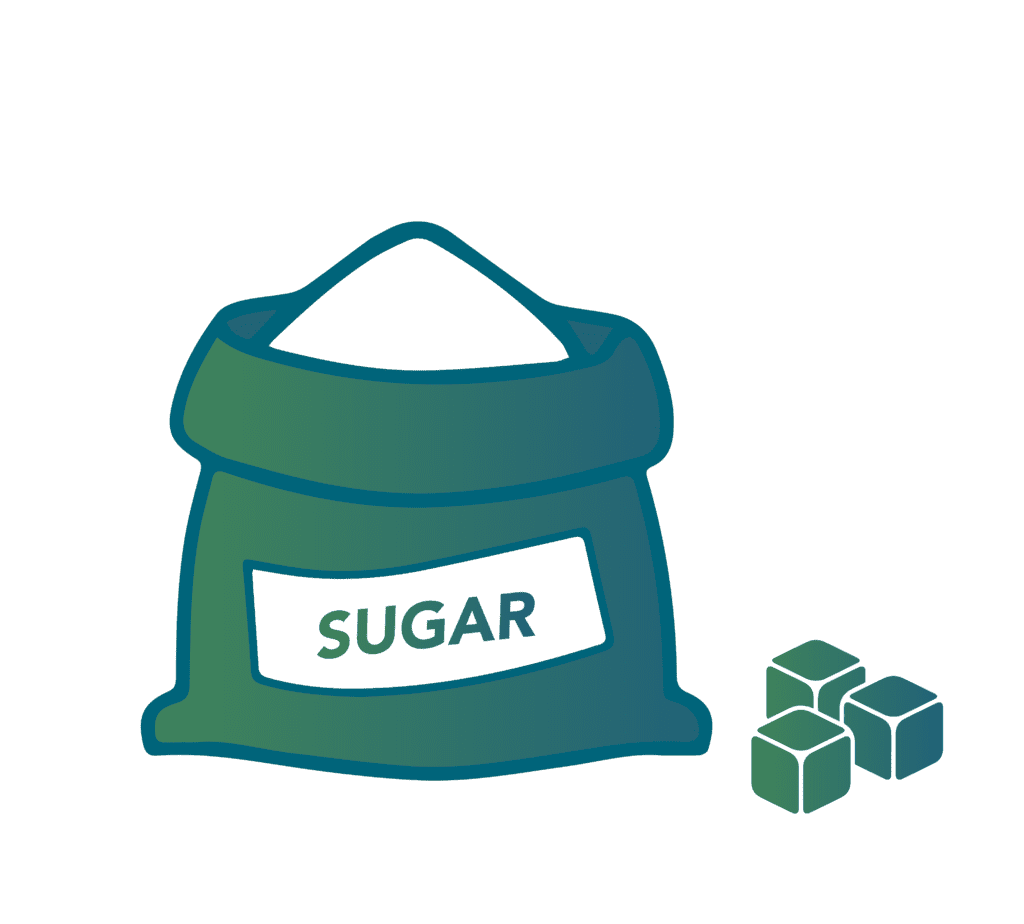
Definition
The difference between the expected material usage and the actual material used in the work order.
Example
If you expected to use 1 lb of sugar but actually used 1 lb 2 oz of sugar.

WO Material Variance (Component Type)
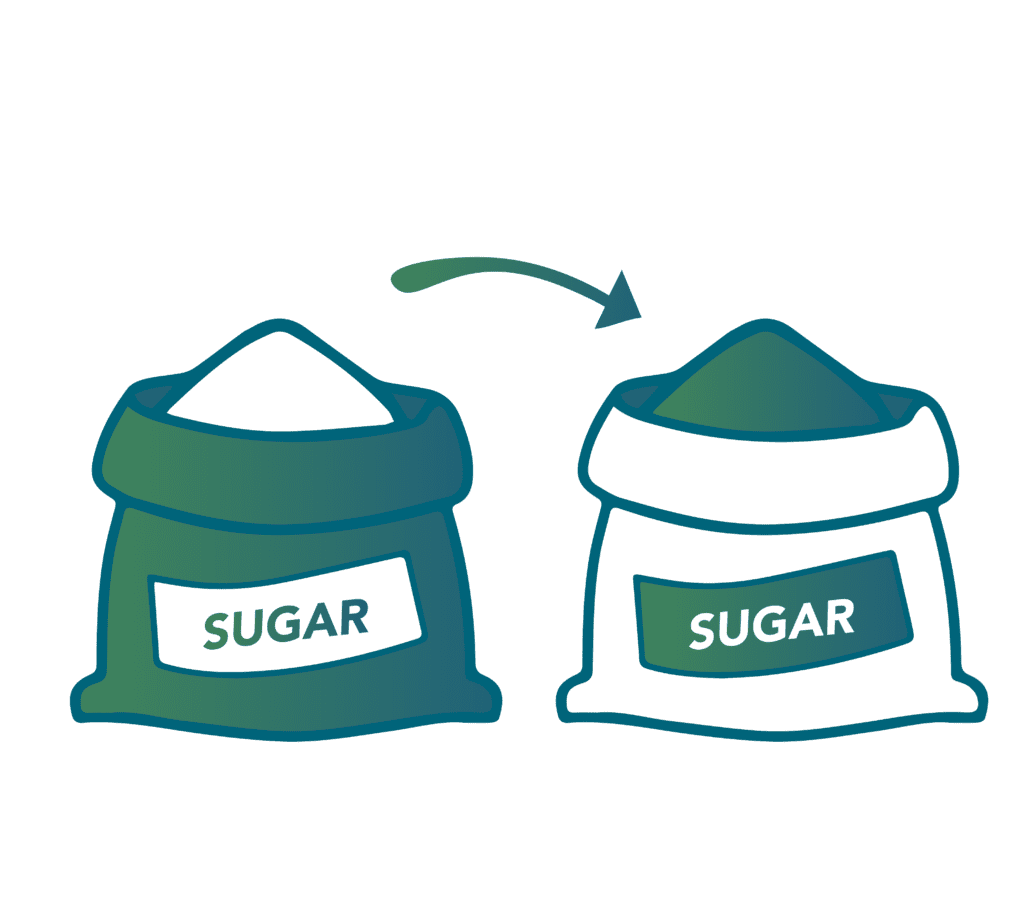
Definition
The difference between the expected type of material used in the work order and the actual material used in the work order.
Example
If you expected to use 1 lb of white sugar but actually used 1 lb of brown sugar.

WO Labor Variance (Usage)
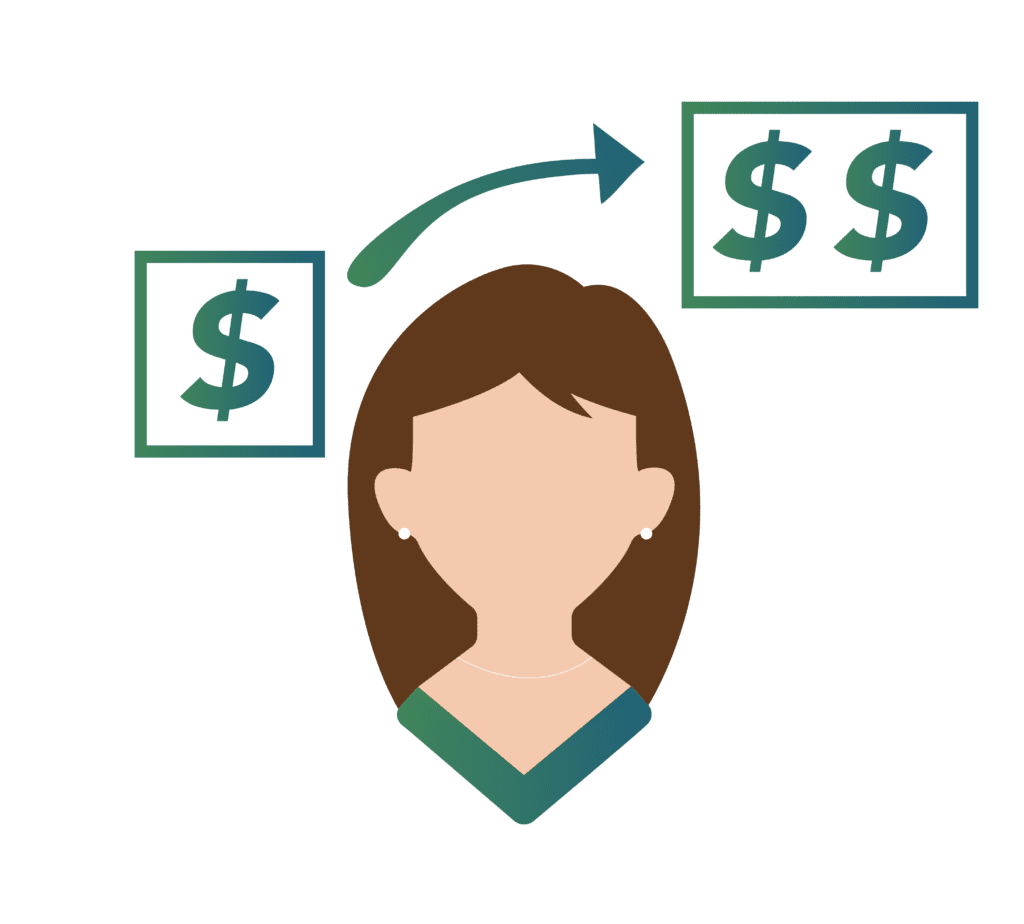
Definition
The difference between the expected time spent and the actual cost of labor used in the work order.
Example
If you expected to spend $1,000 on labor but actually spent $1,200, the labor variance is $200.

WO Labor Variance (Type)
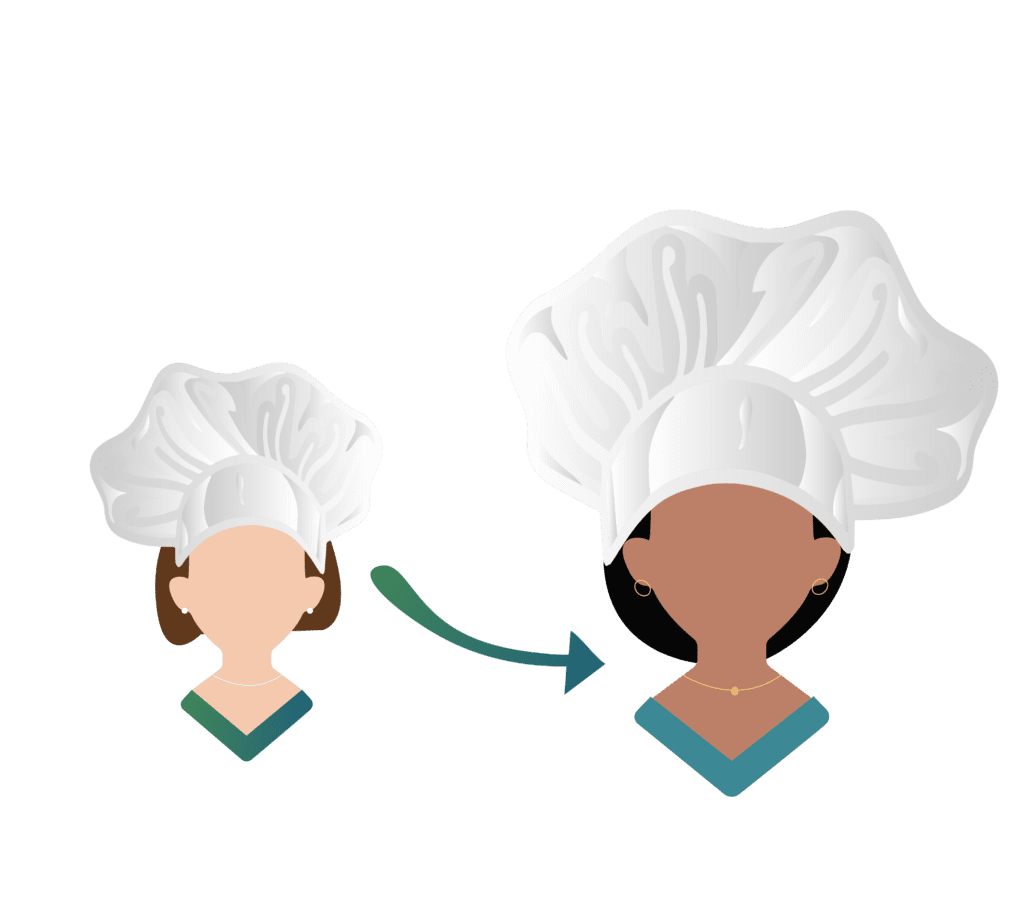
Definition
The difference between the expected labor rate and the actual labor rate in the work order.
Example
If you expected to spend $15/hour for a junior baker but due to availability actually spent $80/hour on a pastry chef.

WO Overhead Variance
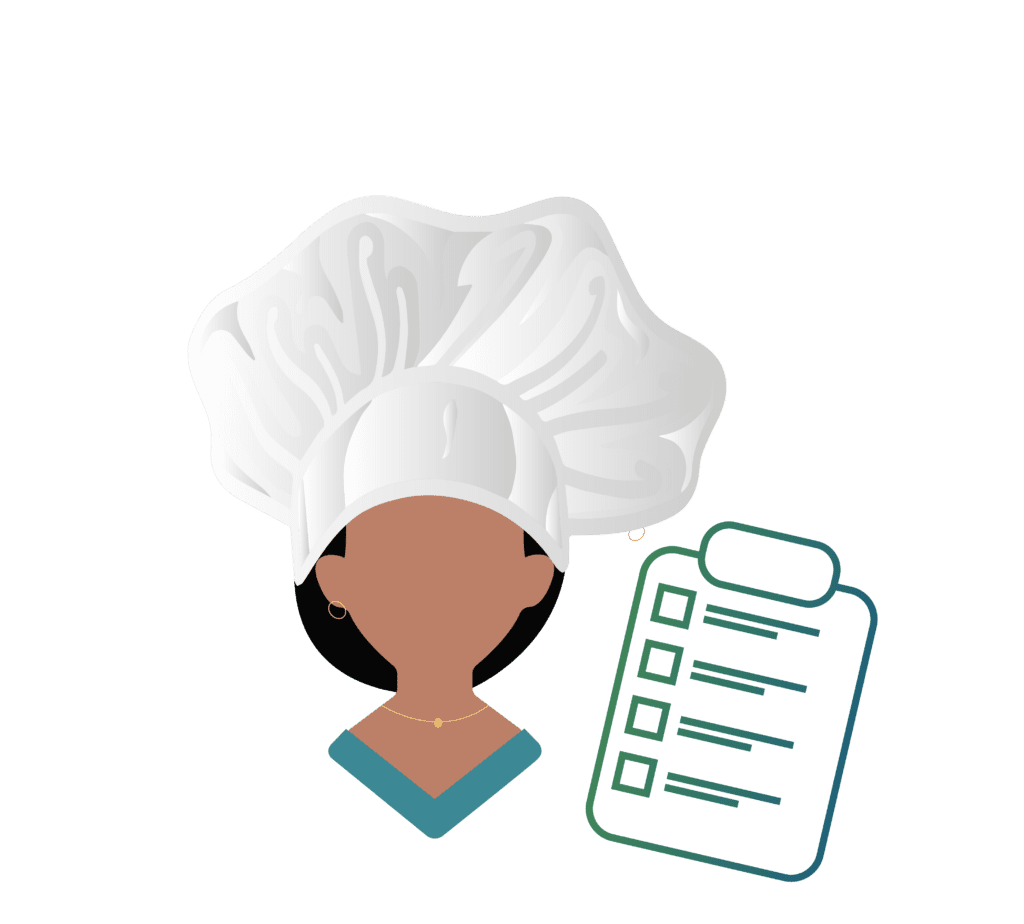
Definition
The difference between standard overhead applied based on the work order and the actual overhead applied. This variance is driven by the burden allocation methodology.
Example
Your standard cost system applies overhead based on labor hours. If the actual labor hours (10 hours) associated with a work order exceed the standard labor hours for a work order (8 hours), overhead will be applied to the work order based on the standard labor hours (8 hours x $16 overhead rate), and the extra 2 labor hours will be captured as a WO Overhead variance (2 hours x $16 overhead rate) on your profit & loss statement.
Other Overhead Variances
In addition to Work Order Overhead Variances, a Work Order Based Standard Cost System will include absorption and spending overhead variances. The WO overhead variance only considers whether the allocation base (labor, machine hours, etc.) based on the standard work order differs between actual. You have to separately consider whether the standard OH rate differs from what would be the actual OH rate, either due to differences between the overall budgeted allocation units (machine or labor hours) or the overall cost of overhead. This is where absorption and spending overhead variances come into play:

Variable Spending Overhead Variance
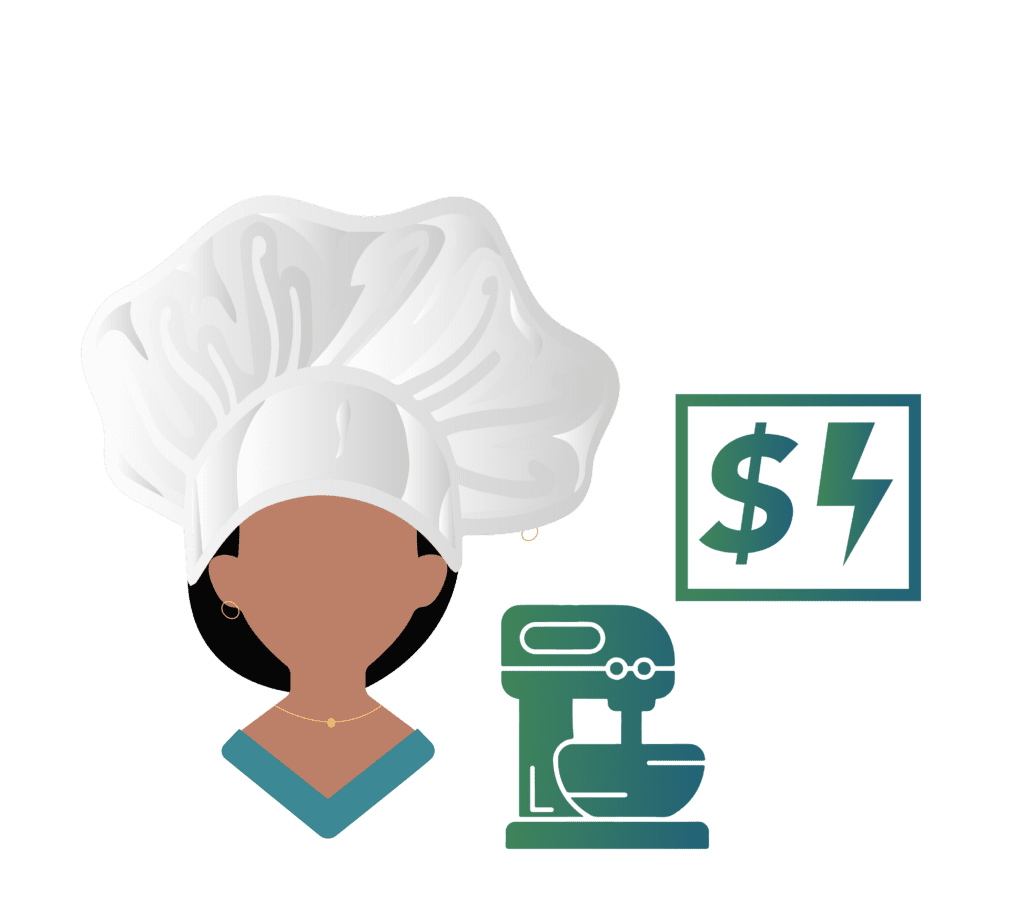
Definition
The difference between what you expected to spend on variable overheads and what you actually spent.
Example
If you expected to spend $2,000 on electricity but actually spent $2,500, the spending variance is $500.

Variable Overhead Efficiency Variance
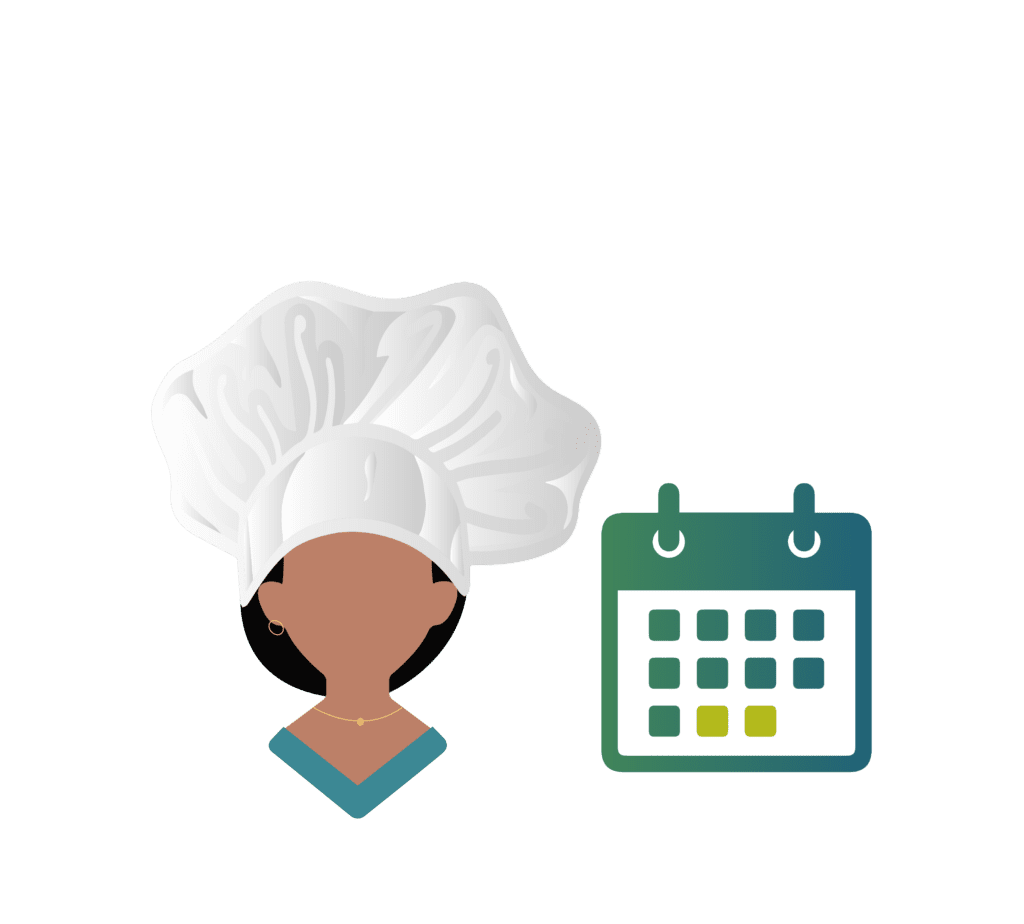
Definition
The difference between the expected and actual usage of the activity base (like machine hours) that drives variable overhead costs.
Example
If you expected to use 100 machine hours but actually used 120 machine hours, the efficiency variance would be based on the cost per machine hours.

Fixed Overhead Budget (Spending) Variance
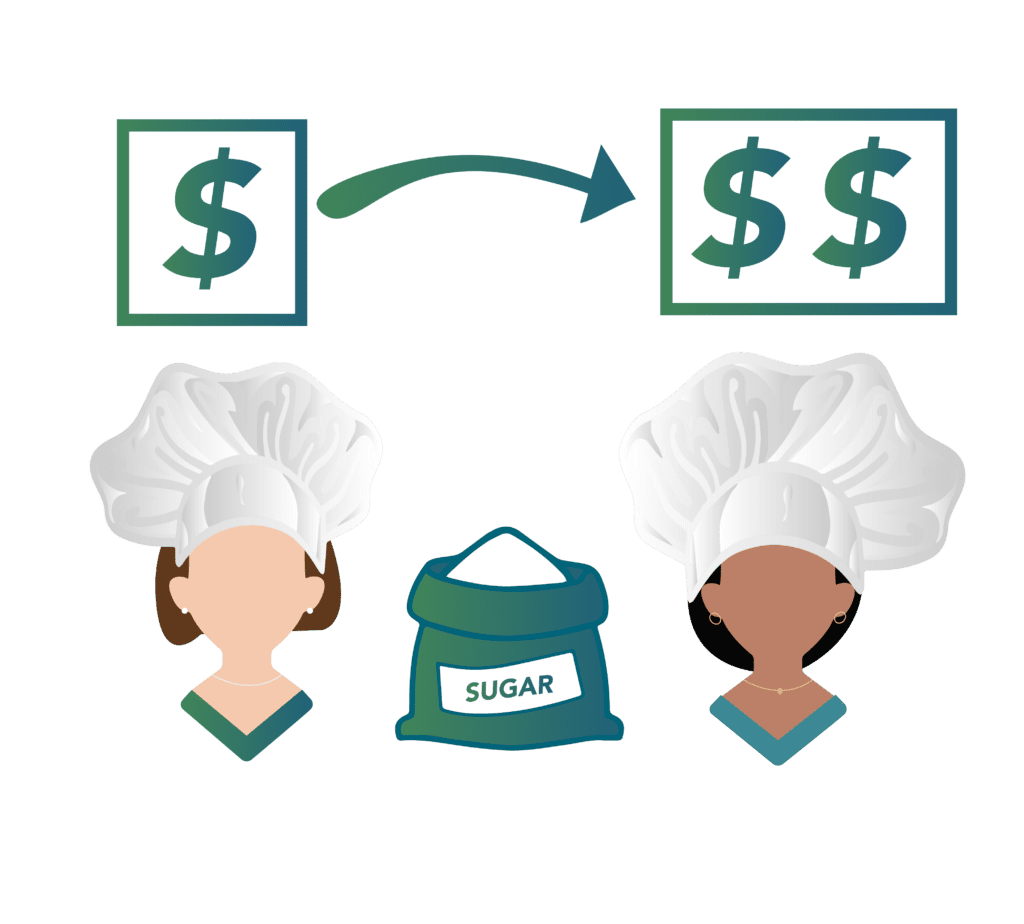
Definition
The difference between the actual fixed overhead costs and the budgeted fixed overhead costs.
Example
If you budgeted $5,000 for rent but actually spent $5,200, the spending variance is $200.

Fixed Overhead Volume Variance
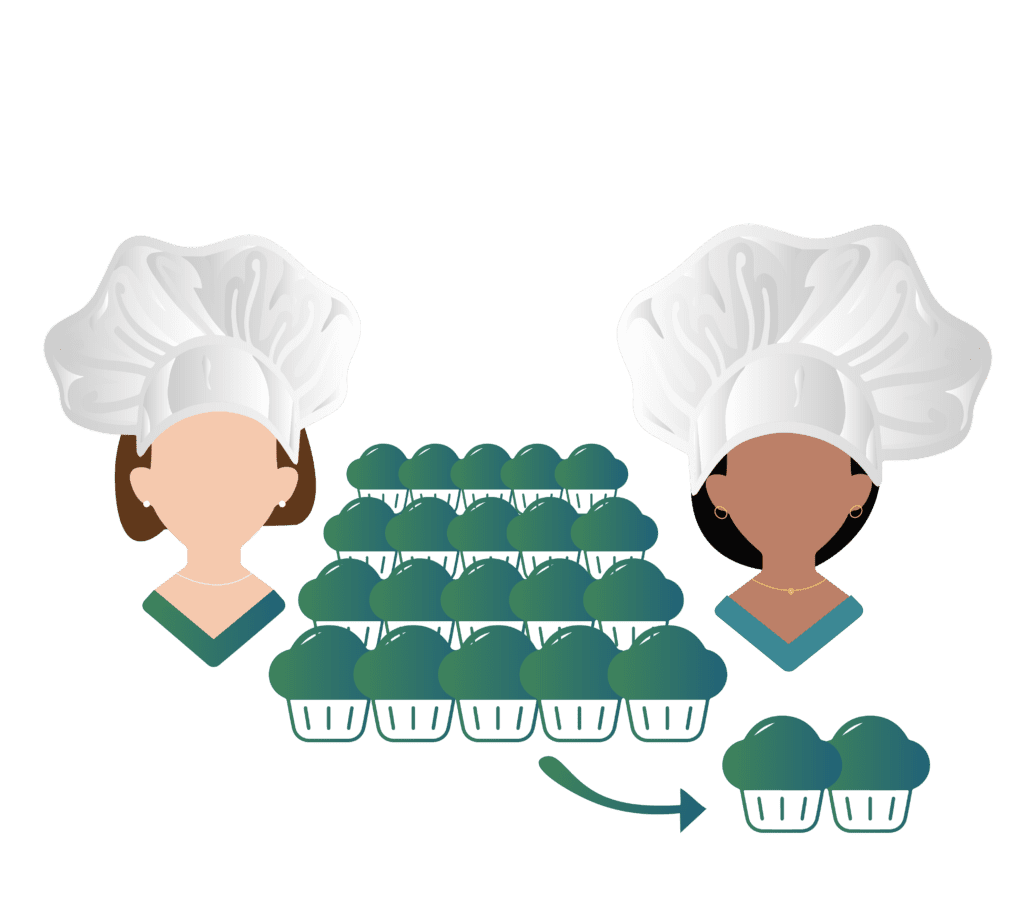
Definition
The difference between the budgeted fixed overhead costs based on standard production levels and the applied (or actual) fixed overhead costs based on actual production levels.
Example
If you budgeted fixed overhead for 1,000 units but actually produced 1,200 units, the volume variance would measure the effect of producing more or fewer units than expected.
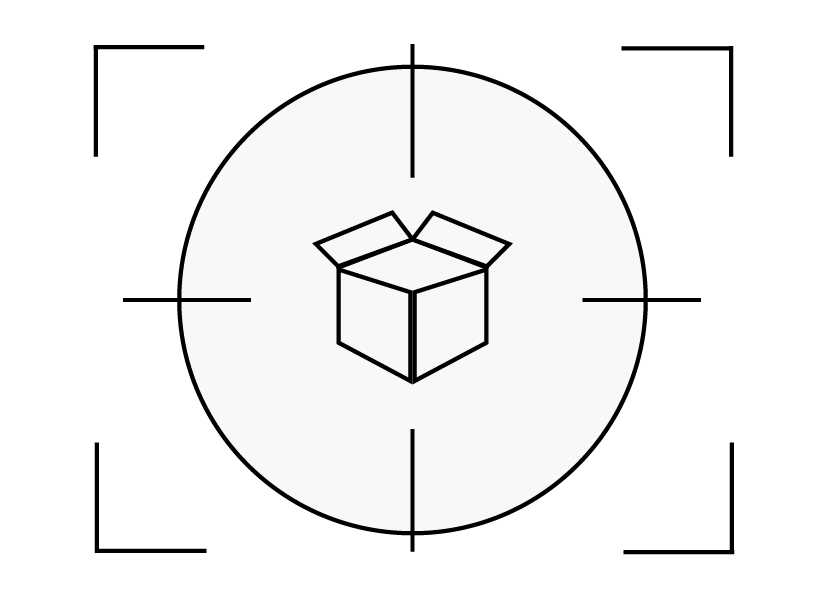
Part II
Estimating Standard Costs
What To Consider
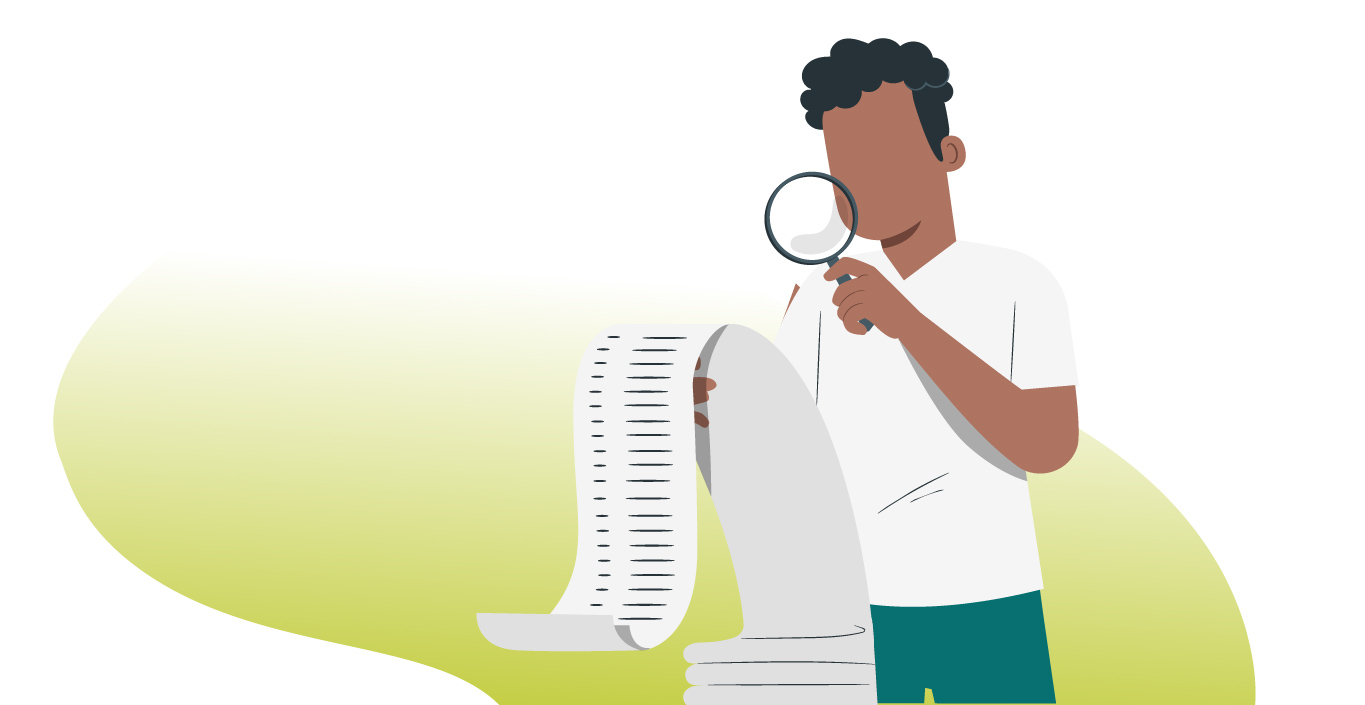
Part III
Defining Cost Variances