Part I: Introduction to the Standard Cost Method
by Izabela Poludniak
The Standard Cost method involves establishing a predetermined cost for each unit of inventory, usually based on historical data or industry standards. This method is best suited for manufacturers who have well-defined production processes and use a standardized set of raw materials and production techniques. By using the Standard Cost method, you get an accurate estimate of the costs associated with producing a product, along with key variance data, which is useful for determining pricing strategies, managing costs, and identifying areas for cost improvement.
What is a Standard Cost?
Think of it as a benchmark or a set expectation for what a particular product or service should cost to produce. It’s like setting a budget for each item or service before you start the actual work. It should generally be based on realistic expectations (often historical data or anticipated purchases) rather than best case scenario.
Why Use a Standard Cost System?
Cost
Control
It helps businesses keep track of their expenses and ensures they don’t overspend.
Performance Measurement
By comparing actual costs with standard costs, businesses can see how well they are managing their resources.
Efficiency Improvement
Identifying where costs differ from the standard helps businesses find areas to improve efficiency.
How Does Inventory Control Work?
First, Set Up Your Accounting System to Value Inventory Using the Standard Cost Method:
If you are implementing an ERP or accounting software for the first time, this is a decision you will want to communicate to your implementation team sooner rather than later. If you want to move to a Standard Cost Method from a different valuation methodology, the decision will likely require engaging a software implementation expert, as it will affect each system differently. The change may not only impact financial reporting, but also production. You will want to understand the impact in order to properly plan and interpret the data produced by the software during the conversion. It’s important to note that in some cases it may take a full inventory cycle for each product or service to fully undergo the conversion process.
Once Your Accounting System is Properly Set Up, Determine Your Standard Costs for Each Particular Product or Service:
Materials
Estimate the cost and volume of raw materials per unit
Labor
Estimate the cost of direct labor, including wages and time needed per unit
Overhead
Estimate the supervisor wages, utilities, rent, etc. per unit and the absorption method (machine hours, labor hours, per unit, etc.)
The total of these costs will equal the unit cost of that particular inventory item on your balance sheet. When the product is sold, the total standard cost will be expensed as Cost of Goods or Services Sold on your Income Statement.
Next, Record Your Actual Costs:
Track the actual expenses incurred during production or service delivery. Ensure that your accounting system and processes capture the actual costs of production including the actual purchase price of raw materials, labor and overhead, as well as the actual time spent to produce a unit and the quantity of raw materials used.
Then Compare Your Costs:
Your accounting system should produce income statements that reflect Cost of Goods Sold based on Standard Cost along with various variance line items that capture the differences between the Cost of Goods Sold (which are valued at Standard Cost) and the actual costs that were incurred during the period.
You will want to analyze the variance accounts to identify whether the variances fall into one of two categories
It’s important to remember that the usefulness of this information is based on the accuracy of your standard cost estimate. Using a standard cost system requires the manufacturer to regularly update standard costs to current estimates. Dated estimates will not only produce less useful variance data but it will also impact the accuracy of your inventory valuation. Remember, under a standard cost system, the balance sheet reflects the value of your inventory at standard cost.
Last But Certainly Not Least:
Investigate significant variances to understand why they occurred and take steps to correct or improve the process.
Unfortunately, the Standard Cost method is not an acceptable inventory valuation method under generally accepted accounting principles (GAAP). If you are issuing financial statements in accordance with GAAP, using the Standard Cost method will require revaluing your year-end inventory based on an accepted GAAP inventory valuation methodology. Such methodologies include First-in-First-Out, average cost, or less commonly, Last-in-First-Out. In some instances, the difference between valuing inventory using a Standard Cost System as opposed to an approved GAAP methodology may not result in a material difference. However, in times of high inflation, deflation, or periods of material or labor scarcity, the difference could be material. It is important to get ahead of any potential valuation issues by revaluing your inventory using an accepted GAAP methodology as part of year-end close.
What are the alternatives to a Standard Cost system?
First-in-First Out (FIFO) is an inventory cost technique that presumes the earliest acquired items are the first to be sold. This approach is best suited for the following types of companies:
- Food Industry: Older food items are likely to be sold before the most recently manufactured or acquired food products
- Pharmaceuticals: Generally pharmaceuticals are sold in order of production, with the oldest expiration date shipping before the most recent
- Retail: Clothing generally ships/sells in order of production, to keep up with changing styles and trends
- Manufacturing: Especially useful for components with limited shelf lives, such as chemicals and electronic components.
The Average Cost Method calculates the value of your inventory based on the average cost of all units purchased. As stated above, this method is best suited for manufacturers who produce products with raw materials that are interchangeable and have similar costs. If you don’t have significant fluctuations in your material or production costs, you can use a simple average cost for your inventory. The Average Cost method can also help you mitigate the effect of large price fluctuations of raw materials.
Last-in-First-Out (LIFO) is less commonly used primarily because most manufacturers avoid holding on to dated inventory. Valuing inventory using LIFO would only appropriately reflect the value of a company’s inventory if the products most recently purchased by the manufacturer are those that are first used in production and sold. This method is more commonly used for tax purposes as a strategy during periods of high inflation.
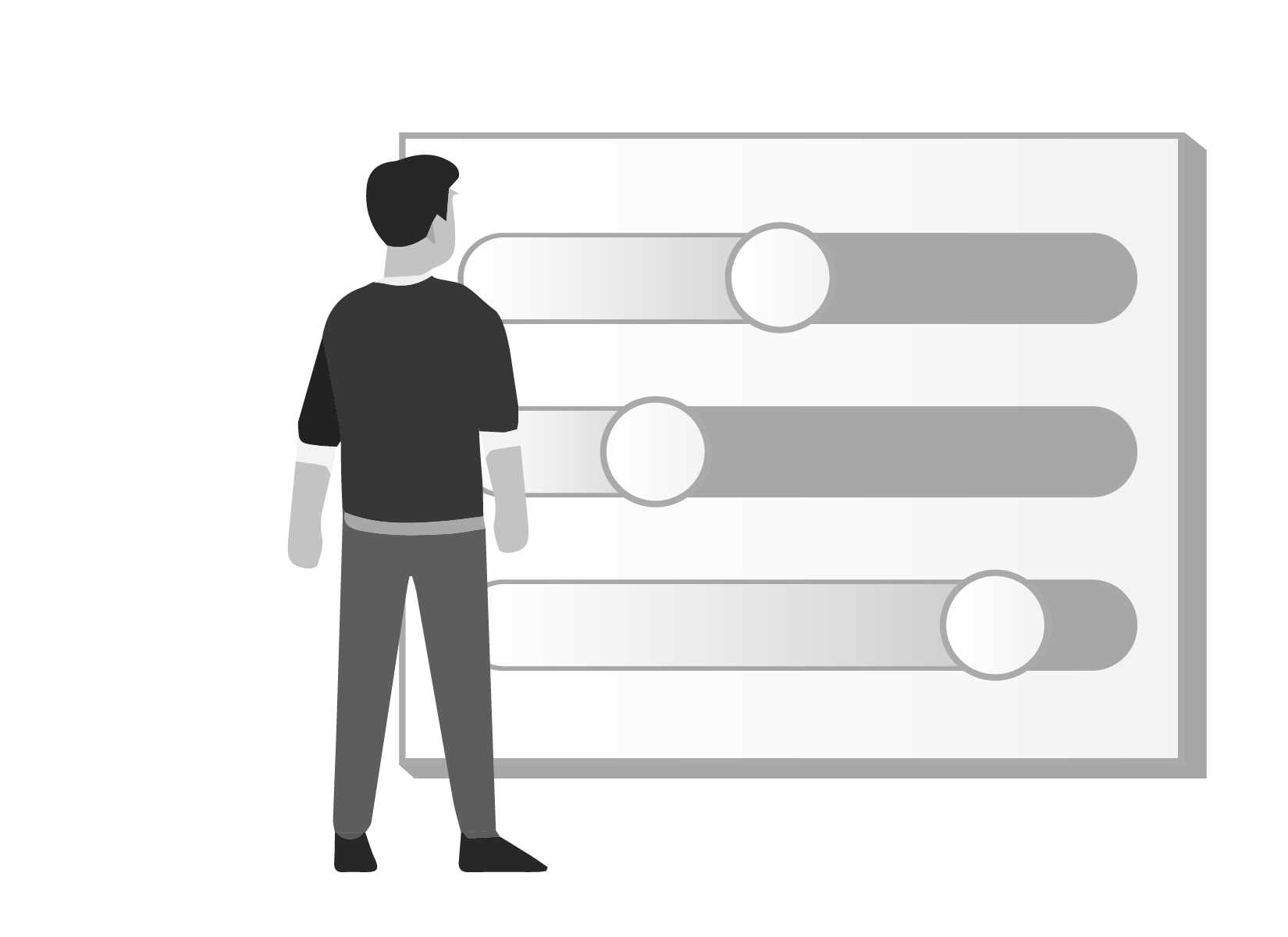
Part II
Estimating Standard Costs –
What to Consider