Inventory management goes beyond simple tracking; it’s about optimizing costs and maximizing resource efficiency. For manufacturers, recognizing the hidden costs of inventory is essential to enhance financial performance and operational efficiency. Here, we delve into these hidden costs and provide actionable strategies to mitigate them.
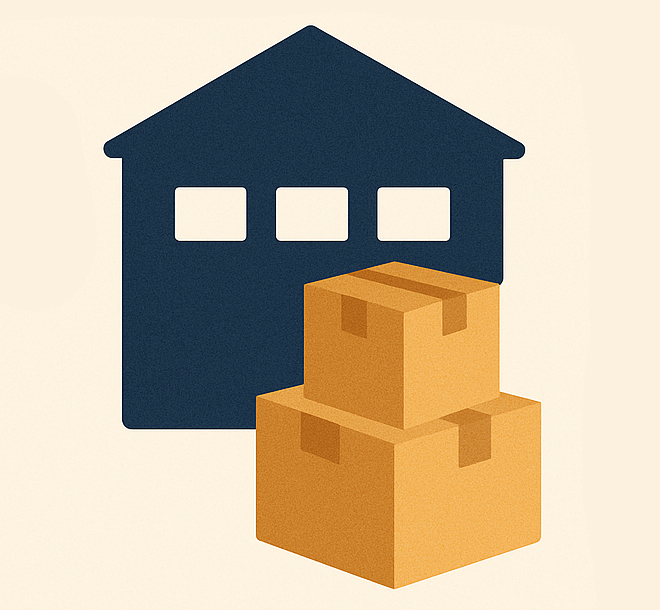
1. Storage Costs
Direct Costs:
Warehousing Expenses: Rent, utilities, and maintenance of storage facilities.
Material Handling: Costs associated with moving inventory in and out of storage.
Indirect Costs:
Opportunity Costs: Capital tied up in inventory could be used elsewhere for investment or operational improvements.
Mitigation Strategies:
Optimize Space Utilization: Use vertical storage solutions and layout optimizations to maximize space. Consideration should also be given to the opportunity cost related to either adding or removing space dedicated to inventory.
Adopt Just-In-Time (JIT) Inventory: Reduce the amount of inventory on hand by ordering only what is necessary to meet immediate demand.
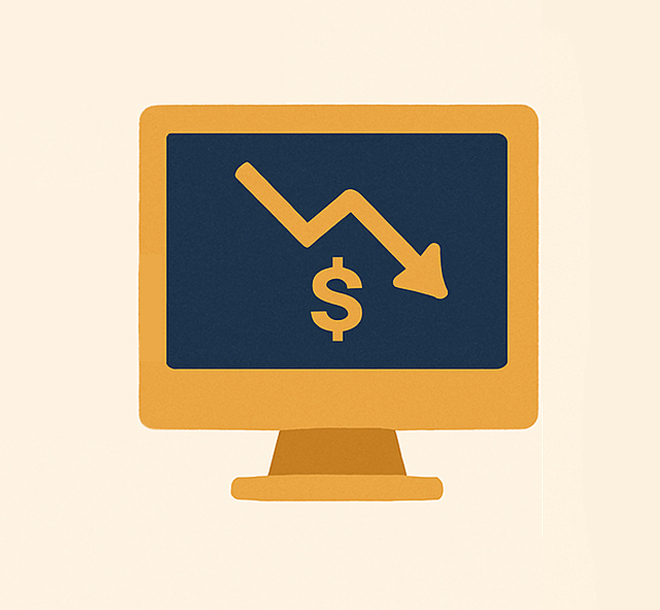
2. Obsolescence and Depreciation
Product Obsolescence:
Technology and consumer preferences evolve rapidly, making some products outdated. This may lead to markdowns or write-offs.
Depreciation:
Over time, the value of inventory can decrease due to wear and tear or market changes.
Mitigation Strategies:
Regular Demand Forecasting: Use predictive analytics to anticipate market trends and adjust inventory levels accordingly.
Product Lifecycle Management: Continuously review product lines and phase out slow-moving or obsolete products.
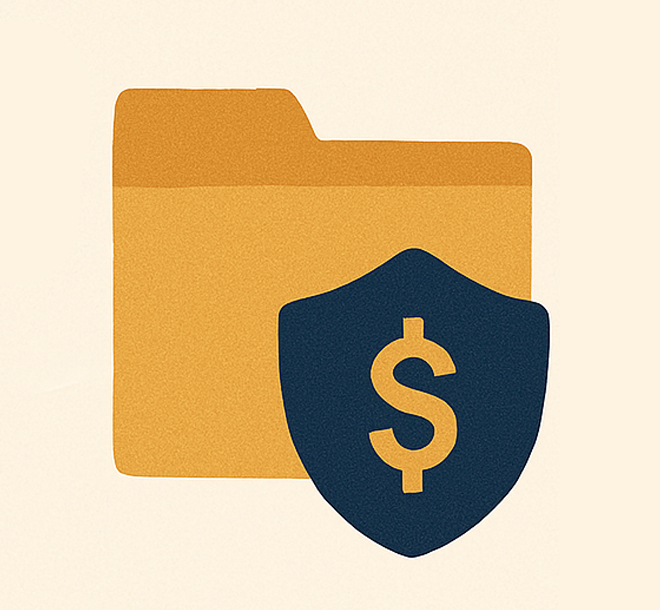
3. Insurance and Taxes
Insurance Premiums:
Higher inventory levels can lead to increased insurance costs.
Inventory Taxes:
Some jurisdictions impose taxes based on the value of inventory on hand.
Mitigation Strategies:
Inventory Optimization: Maintain optimal but minimal inventory levels to minimize insurance and tax liabilities.
Review Insurance Policies: Periodically assess insurance needs and negotiate better terms with providers.
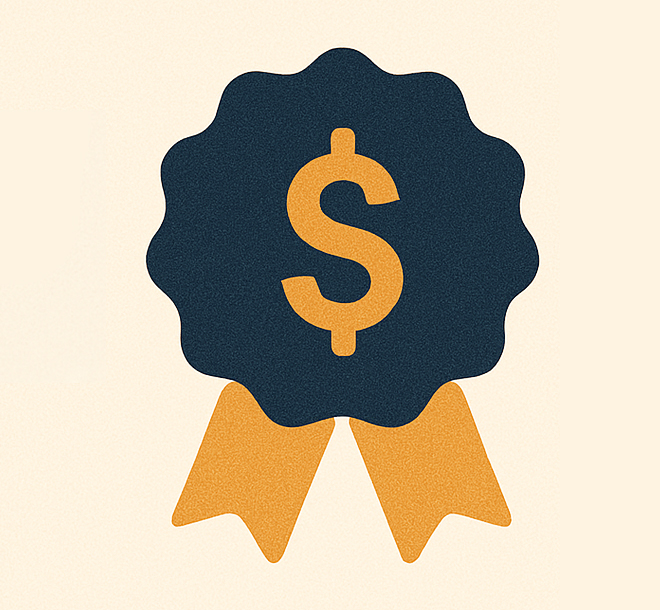
4. Quality Costs
Inspection Costs:
Regular quality checks are necessary to ensure inventory meets standards.
Defective Goods:
Costs incurred from returns, repairs, or replacements.
Mitigation Strategies:
Supplier Quality Management: Work closely with suppliers to ensure quality standards are met before products reach your facility.
Implement Quality Control Measures: Integrate automated inspection systems to reduce manual errors and enhance efficiency. Additional procedures would likely be necessary with delivery of aged inventory to ensure quality products are provided to customers.
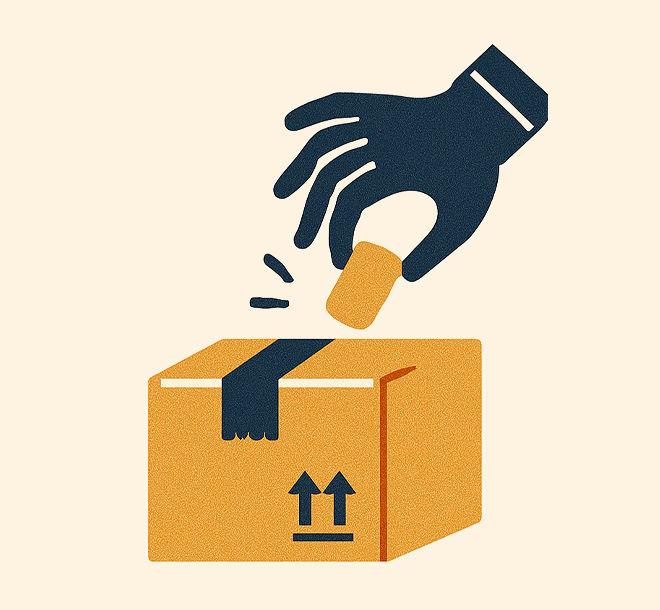
5. Shrinkage and Theft
Shrinkage:
Losses due to theft, fraud, or clerical errors can be significant.
Security Measures:
Investments in security systems and personnel to prevent theft.
Mitigation Strategies:
Advanced Security Systems: Employ CCTV, access controls, and alarm systems to deter theft.
Regular Inventory Audits: Conduct random audits to detect discrepancies early and address potential issues promptly.
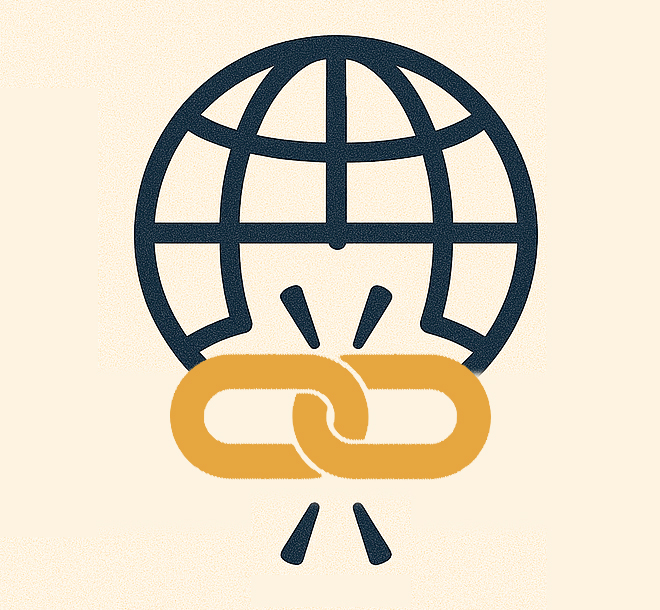
6. Supply Chain Disruptions
Fluctuating Demand:
Economic shifts or unforeseen events can result in excess inventory or stockouts.
Supplier Reliability:
Issues with suppliers can cause delays and additional costs in expediting orders.
Mitigation Strategies:
Diversify Supplier Base: Reduce reliance on a single supplier by working with multiple vetted suppliers.
Flexible Contract Terms: Negotiate adaptable terms to adjust orders based on fluctuating demands.
By implementing a variety of these strategies, manufacturers can reduce the additional costs incurred withholding excessive inventories. Effective inventory management not only improves financial reporting accuracy but also boosts operational efficiency and competitive advantage. This allows for more accurate data-driven decision-making and ultimately drives sustainable growth for manufacturing organizations.